Discrete Event Simulation (DES) is a powerful tool for process optimization, allowing organizations to model, analyze, and improve complex systems. By simulating the sequence of events in a process, businesses can identify bottlenecks, test scenarios, and implement changes without disrupting real-world operations. This article provides a comprehensive exploration of DES, its benefits, key features, and practical examples to enhance understanding.
What Is Discrete Event Simulation in Process Optimization?
Discrete Event Simulation in process optimization is a computational modeling technique that represents the operation of a system as a chronological sequence of events. Each event occurs at a specific point in time and marks a change of state in the system. The reason DES is essential is that it enables the analysis of complex processes where interactions and variability are significant. For example, in manufacturing, DES can simulate a production line to identify inefficiencies and optimize throughput.
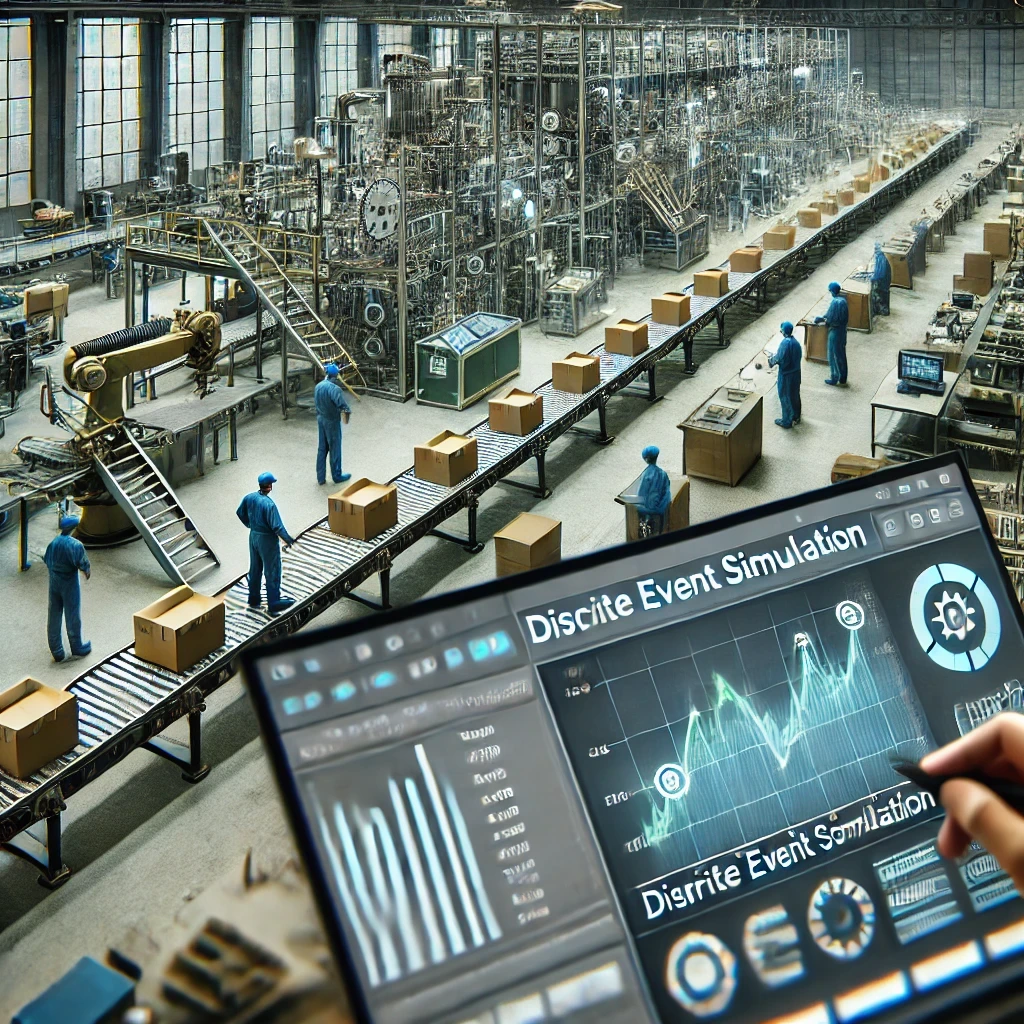
How Does Discrete Event Simulation Work?
Understanding how Discrete Event Simulation works involves recognizing its core components:
- Entities: Objects or components within the system (e.g., machines, products).
- Events: Occurrences that change the state of entities (e.g., machine breakdowns).
- Resources: Elements required for processes (e.g., labor, materials).
- Queues: Waiting lines where entities reside before processing.
DES operates by progressing through simulated time, processing events in chronological order. When an event occurs, the system state updates accordingly. For instance, if a machine completes a task at time T, the simulation records this and moves the entity to the next process step. This mechanism allows for detailed analysis of process dynamics.
Why Is Discrete Event Simulation Important for Process Optimization?
Discrete Event Simulation is important for process optimization because it provides insights into system behavior under various conditions. By modeling processes, organizations can:
- Identify Bottlenecks: Detect stages causing delays.
- Test Scenarios: Evaluate the impact of changes without real-world risks.
- Optimize Resource Allocation: Determine optimal staffing and equipment use.
- Reduce Costs: Minimize waste and improve efficiency.
For example, a logistics company might use DES to simulate warehouse operations, discovering that rearranging storage locations reduces picking times by 15%.
What Are the Key Benefits of Using Discrete Event Simulation?
The key benefits of using Discrete Event Simulation include:
- Enhanced Decision-Making: Provides data-driven insights for strategic planning.
- Risk Reduction: Allows testing changes virtually before implementation.
- Cost Savings: Identifies inefficiencies leading to cost reductions.
- Improved Productivity: Optimizes processes to increase output.
- Flexibility: Adapts to various industries and process types.
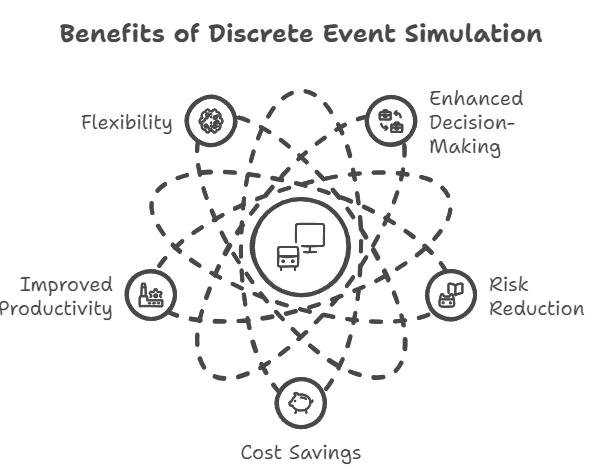
A 2019 study published in the International Journal of Production Research found that companies implementing DES experienced an average productivity increase of 20%.
Which Industries Benefit Most from Discrete Event Simulation?
Industries that benefit most from Discrete Event Simulation are those with complex, variable processes, including:
- Manufacturing: Streamlining production lines.
- Healthcare: Optimizing patient flow in hospitals.
- Logistics and Supply Chain: Enhancing warehouse operations and transportation.
- Telecommunications: Managing network traffic and service provisioning.
- Service Industries: Improving customer service processes.
For instance, in healthcare, DES has been used to reduce patient waiting times by simulating appointment schedules and resource allocation.
How Does Descar.Tech Utilize Discrete Event Simulation?
Descar.Tech specializes in the design and simulation of industrial processes, focusing on optimizing production through technological innovation. Utilizing Discrete Event Simulation, Descar.Tech offers:
- Virtual Modeling of Production Lines: Creating digital twins to test different scenarios.
- Identification of Bottlenecks: Analyzing process flows to pinpoint inefficiencies.
- Process Automation: Implementing automated solutions for enhanced productivity.
- Customized Solutions: Tailoring simulations to specific client needs.
By employing tools like Siemens PLM software, Descar.Tech helps clients increase efficiency, reduce costs, and improve project quality.
What Are the Steps to Implement Discrete Event Simulation for Process Optimization?
Implementing Discrete Event Simulation involves several steps:
- Define Objectives: Establish clear goals for the simulation.
- Collect Data: Gather accurate process data (e.g., processing times, arrival rates).
- Build the Model: Use simulation software to create the process model.
- Validate the Model: Ensure the model accurately represents the real system.
- Run Simulations: Execute scenarios to analyze outcomes.
- Analyze Results: Interpret data to identify improvements.
- Implement Changes: Apply findings to optimize the actual process.
For example, a manufacturing plant might follow these steps to reduce cycle time, resulting in a 10% increase in production capacity.
What Software Tools Are Commonly Used for Discrete Event Simulation?
Common software tools for Discrete Event Simulation include:
- Siemens Plant Simulation: Offers advanced modeling for complex systems.
- Arena Simulation: Widely used in academia and industry for various applications.
- Simul8: User-friendly interface suitable for quick model development.
- AnyLogic: Supports multi-method modeling including DES, agent-based, and system dynamics.
These tools provide features like drag-and-drop modeling, statistical analysis, and 3D visualization to facilitate the simulation process.
How Does Discrete Event Simulation Compare to Other Simulation Methods?
Comparing Discrete Event Simulation to other methods highlights its unique advantages:
- Continuous Simulation: Models systems where changes occur continuously over time, suitable for fluid dynamics. DES focuses on discrete events.
- Agent-Based Simulation: Simulates interactions of autonomous agents; DES is process-oriented.
- Monte Carlo Simulation: Uses random sampling for probabilistic analysis; DES models sequence of events with specific logic.
DES is particularly effective for systems where state changes happen at specific points in time, making it ideal for process optimization.
What Are Real-World Examples of Discrete Event Simulation Improving Processes?
Real-world examples include:
- Automotive Manufacturing: A plant reduced assembly line downtime by 25% in 2020 by simulating maintenance schedules.
- Airport Operations: Simulations helped optimize passenger flow, decreasing boarding times by 15%.
- Call Centers: DES enabled a company to adjust staffing levels, improving customer satisfaction scores by 12%
These cases demonstrate the tangible benefits of applying DES in various sectors.
How Does Discrete Event Simulation Support Industrial Automation?
Discrete Event Simulation supports industrial automation by:
- Modeling Automated Systems: Simulating the integration of robotics and machinery.
- Optimizing Control Logic: Testing and refining automated process controls.
- Enhancing System Design: Evaluating the impact of automation on overall workflow.
Descar.Tech leverages DES to implement automation solutions, ensuring seamless integration and maximum efficiency. Learn more at Descar.Tech’s article on Industrial Automation.
How Can Discrete Event Simulation Aid in Design for Manufacturing?
In Design for Manufacturing (DFM), DES aids by:
- Evaluating Manufacturability: Testing product designs within simulated production processes.
- Identifying Design Constraints: Recognizing potential manufacturing issues early.
- Optimizing Production Strategies: Aligning design decisions with process capabilities.
By incorporating DES in DFM, companies can reduce time-to-market and production costs. For further insights, visit Descar.Tech’s article on Design for Manufacturing.
What Is the Role of Discrete Event Simulation in Plant Simulation?
In plant simulation, Discrete Event Simulation plays a critical role by:
- Creating Digital Twins: Developing virtual replicas of entire facilities.
- Testing Layouts: Assessing different configurations for optimal flow.
- Forecasting Performance: Predicting outcomes under various conditions.
Descar.Tech excels in plant simulation, helping clients design and model industrial plants effectively. Explore more at Descar.Tech’s article on Plant Simulation.
How Does Discrete Event Simulation Integrate with Advanced Planning and Scheduling Systems?
DES integrates with Advanced Planning and Scheduling (APS) systems by:
- Providing Detailed Process Models: Enhancing scheduling accuracy.
- Simulating Scheduling Scenarios: Evaluating the impact of different plans.
- Improving Resource Utilization: Aligning schedules with process capabilities.
This integration leads to better coordination and efficiency. For beginners, Descar.Tech offers an overview of APS systems.
What Are the Challenges in Implementing Discrete Event Simulation?
Challenges include:
- Data Quality: Requires accurate and comprehensive data.
- Complexity: Models can become intricate, needing expertise.
- Resource Investment: Time and cost to build and validate models.
Overcoming these challenges involves proper planning, training, and potentially partnering with experts like Descar.Tech.
How Can Companies Get Started with Discrete Event Simulation?
Companies can get started by:
- Assessing Needs: Identify processes that could benefit from DES.
- Choosing the Right Tool: Select software that fits their requirements.
- Building Expertise: Train staff or hire specialists.
- Starting Small: Begin with a pilot project.
- Partnering with Experts: Collaborate with firms like Descar.Tech for guidance.
Taking these steps facilitates a successful implementation of DES for process optimization.
Frequently Asked Questions
What Is the Difference Between Discrete Event Simulation and Continuous Simulation?
Discrete Event Simulation models systems where changes occur at specific events, while Continuous Simulation models changes continuously over time. DES is suitable for process flows, whereas continuous simulation applies to phenomena like fluid dynamics.
How Accurate Are Discrete Event Simulation Models?
The accuracy depends on the quality of input data and model validation. Properly calibrated models can closely represent real-world processes, providing reliable insights.
Can Discrete Event Simulation Be Used in Small Businesses?
Yes, DES can benefit businesses of all sizes by identifying inefficiencies and optimizing processes, leading to cost savings and productivity gains.
What Skills Are Needed to Implement Discrete Event Simulation?
Skills include understanding of the process being modeled, proficiency with simulation software, and analytical abilities to interpret results.
How Long Does It Take to Develop a Discrete Event Simulation Model?
Development time varies based on complexity but can range from a few weeks for simple models to several months for complex systems.
Is Discrete Event Simulation Cost-Effective?
While there is an initial investment, the long-term benefits of optimized processes often result in a high return on investment.
How Does Discrete Event Simulation Handle Randomness in Processes?
DES incorporates stochastic elements by using probability distributions to model variability in processes, such as arrival times or service durations.
Can Discrete Event Simulation Be Integrated with Other Technologies?
Yes, DES can be integrated with technologies like IoT devices, ERP systems, and data analytics platforms for enhanced functionality.
What Industries Are Emerging Users of Discrete Event Simulation?
Emerging industries include renewable energy for grid management and biotechnology for process development.
How Can Descar.Tech Assist with Discrete Event Simulation Projects?
Descar.Tech offers expertise in designing and simulating industrial processes using DES, providing customized solutions to optimize production. Their services include virtual modeling, bottleneck identification, and automation implementation.
By leveraging Discrete Event Simulation, organizations can gain valuable insights into their processes, leading to significant improvements in efficiency and profitability. With the support of experts like Descar.Tech, implementing DES becomes a strategic advantage in today’s competitive landscape.
Contact our advisors at https://descar.tech/#contact
Recent Comments