Introduction to APS Systems: Navigating Modern Manufacturing
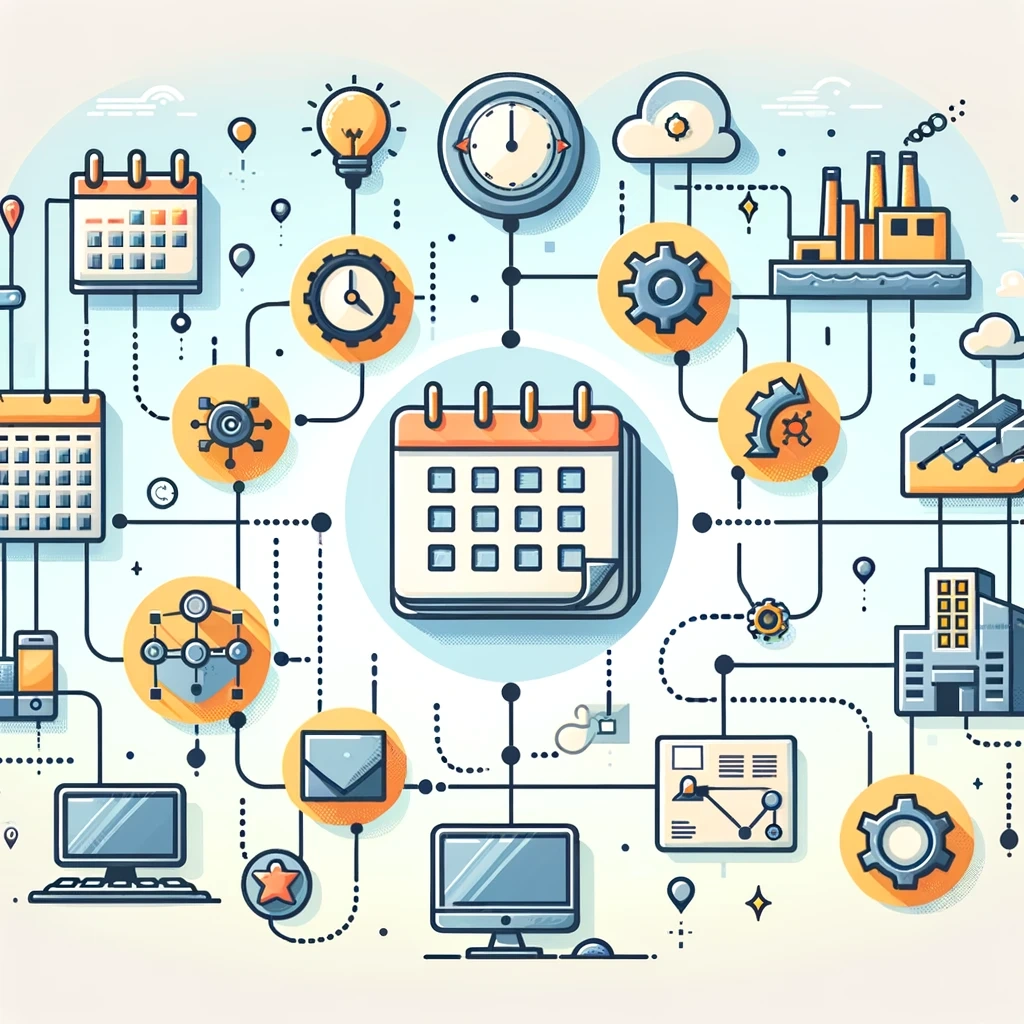
Unveiling Advanced Planning and Scheduling (APS)
In the intricate world of modern manufacturing, Advanced Planning and Scheduling (APS) systems have emerged as pivotal tools. These systems represent a significant leap from traditional production planning methods, introducing a new era of efficiency and optimization in manufacturing processes.
APS: The Heartbeat of Contemporary Manufacturing
APS systems are the linchpins in modern manufacturing, orchestrating the complex interplay between various production elements. They are designed to manage and optimize the use of resources, balance supply with demand, and streamline production schedules. This ensures that manufacturers can respond swiftly and effectively to market changes and production dynamics.
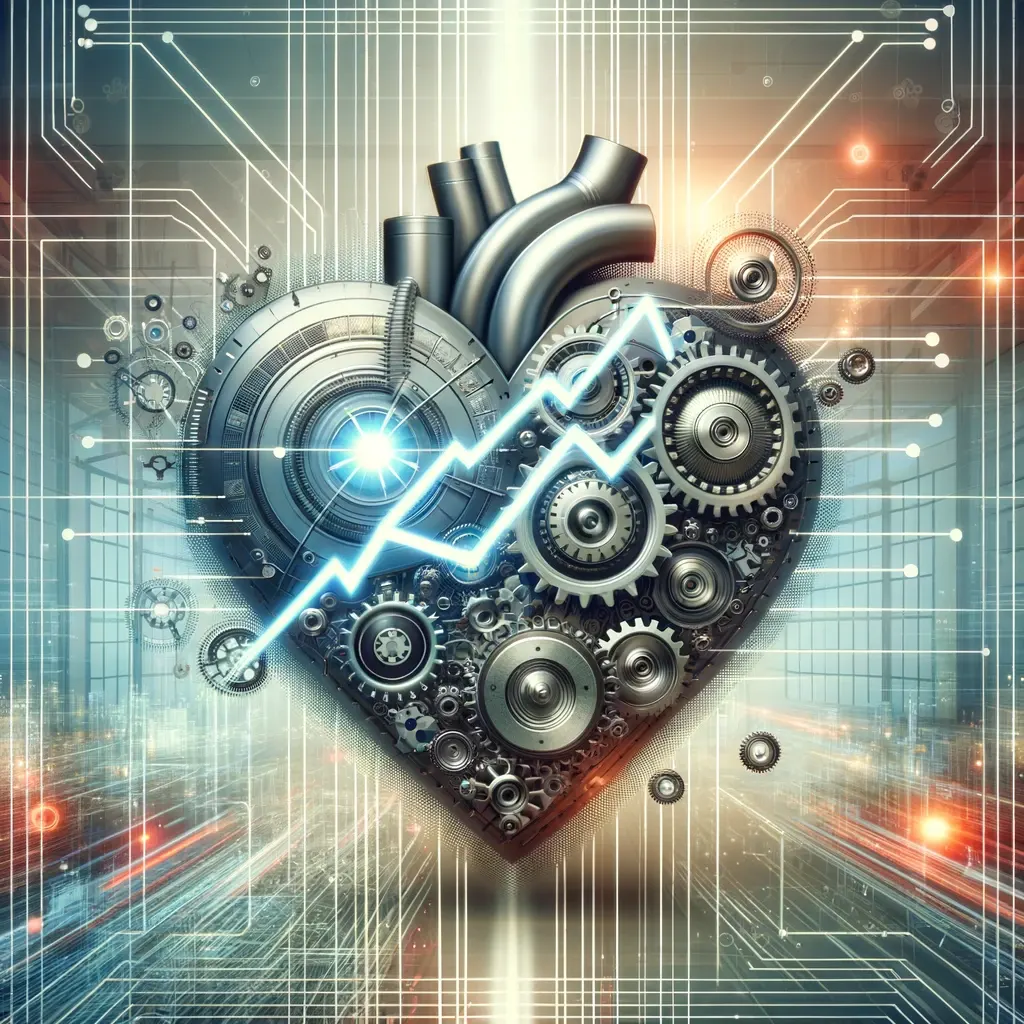
A Paradigm Shift in Production Planning
The advent of APS marked a paradigm shift in how manufacturing entities approach production planning. Moving away from the reactive and often rigid traditional methods, APS introduces a proactive, flexible, and integrated approach. This shift is crucial in today’s fast-paced, demand-driven market where adaptability and responsiveness are key to maintaining a competitive edge.
The Relevance of APS in Today’s Manufacturing
In today’s manufacturing landscape, characterized by rapid technological advancements and evolving consumer demands, APS systems stand as critical enablers. They allow manufacturers to not only keep pace with market changes but also to anticipate and prepare for future trends, thereby optimizing their operational efficiency and productivity.
In this overview, we will delve into the key components of APS systems, exploring how they transform the complexities of modern manufacturing into streamlined processes that drive success and innovation.
Demand Forecasting: Predicting Market Needs in APS
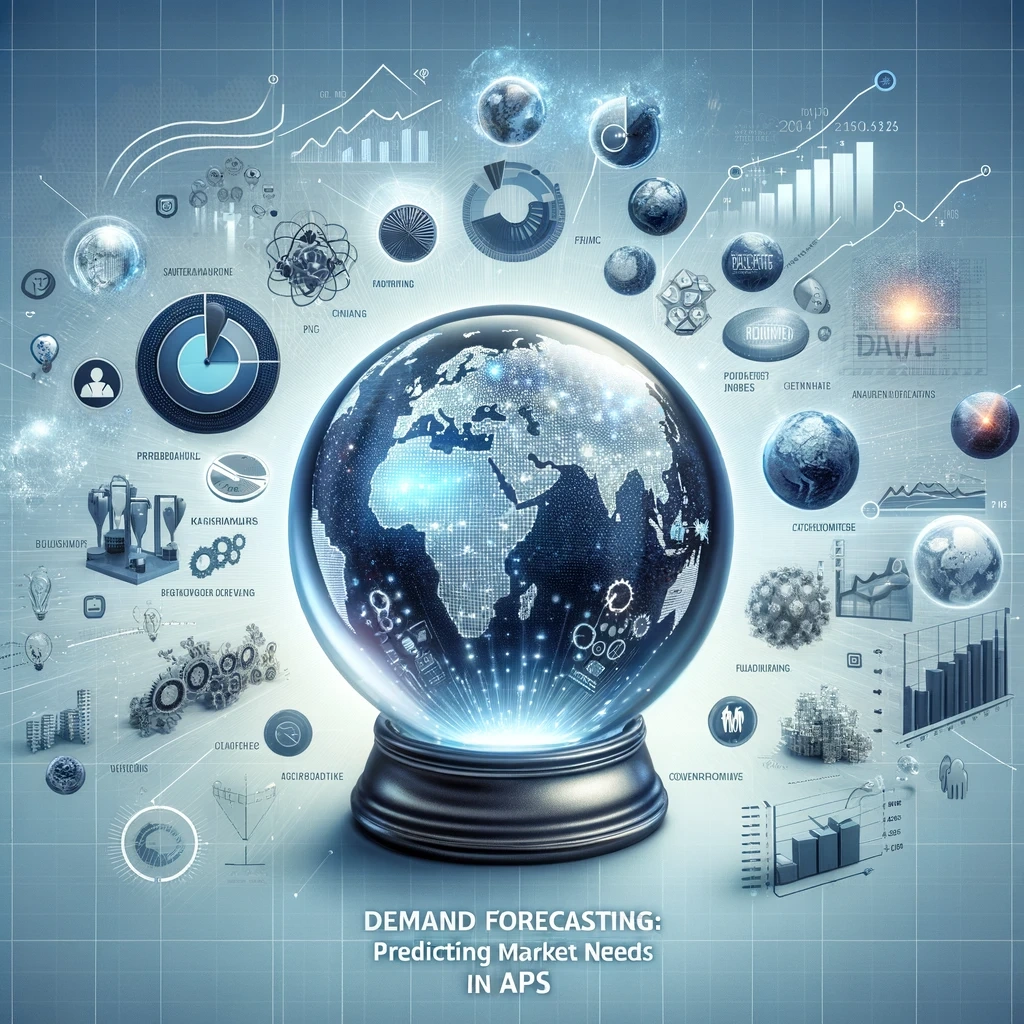
The Role of Demand Forecasting in APS
Demand forecasting stands at the forefront of the Advanced Planning and Scheduling (APS) process. It is the strategic component that predicts future customer demands, enabling manufacturers to align their production plans accordingly. This predictive element is crucial for ensuring that production meets market needs efficiently without leading to overproduction or shortages.
The Mechanics of Demand Forecasting in APS
Demand forecasting within APS uses a blend of historical data analysis and predictive modeling. By analyzing past sales trends, seasonal fluctuations, and market changes, APS systems can forecast future demand with a high degree of accuracy. This data-driven approach is enhanced by modern technologies such as machine learning and AI, which refine predictive models for even more precise forecasting.
Impact on Production Planning
The influence of demand forecasting on production planning is profound. Accurate forecasts enable manufacturers to make informed decisions about resource allocation, inventory management, and production scheduling. This proactive planning reduces the risk of stockouts or excess inventory, optimizing resource utilization and minimizing waste. In essence, demand forecasting acts as a compass, guiding the entire production process towards market-aligned efficiency.
Resource Allocation: Maximizing Efficiency in APS
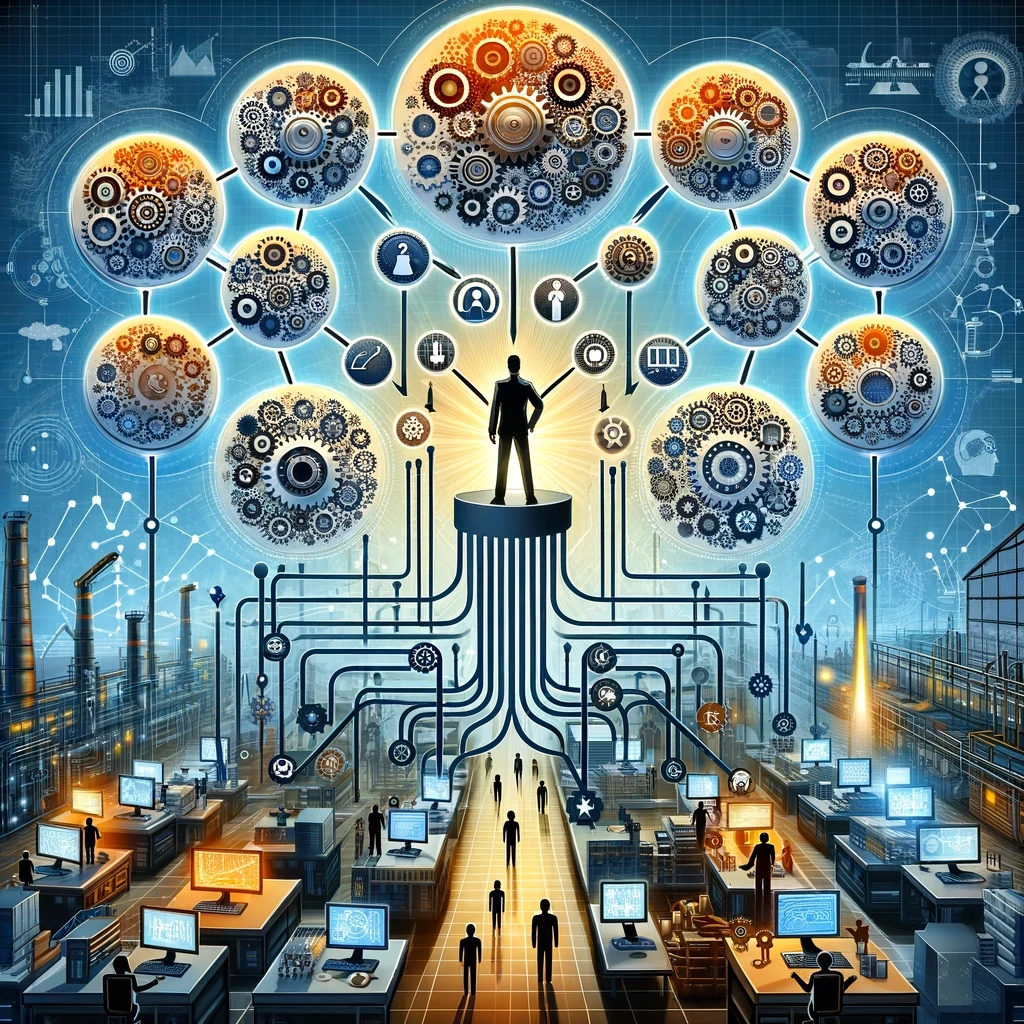
The Essence of Resource Allocation in APS
Resource allocation within Advanced Planning and Scheduling (APS) systems is a critical process that aligns available resources with production needs. This component of APS is essential for maximizing operational efficiency and productivity in manufacturing settings.
Strategizing Resource Utilization
APS systems strategically manage and distribute resources, including manpower, machinery, and materials. By analyzing production demands and resource availability, APS ensures that resources are utilized effectively, reducing instances of underutilization or overburdening. This strategic allocation is pivotal in maintaining a seamless production flow.
Balancing Act: Aligning Resources with Production
The primary goal of resource allocation in APS is to achieve a balance between available resources and production requirements. APS systems consider various factors such as capacity constraints, maintenance schedules, and workforce availability. This balance is crucial to avoid bottlenecks and ensure that production targets are met efficiently.
Resource allocation in APS is more than just a logistical task; it’s a strategic decision-making process that significantly impacts the efficiency and productivity of manufacturing operations. By effectively aligning resources with production needs, APS systems play a vital role in optimizing manufacturing processes.
Scheduling: Orchestrating the Manufacturing Process in APS
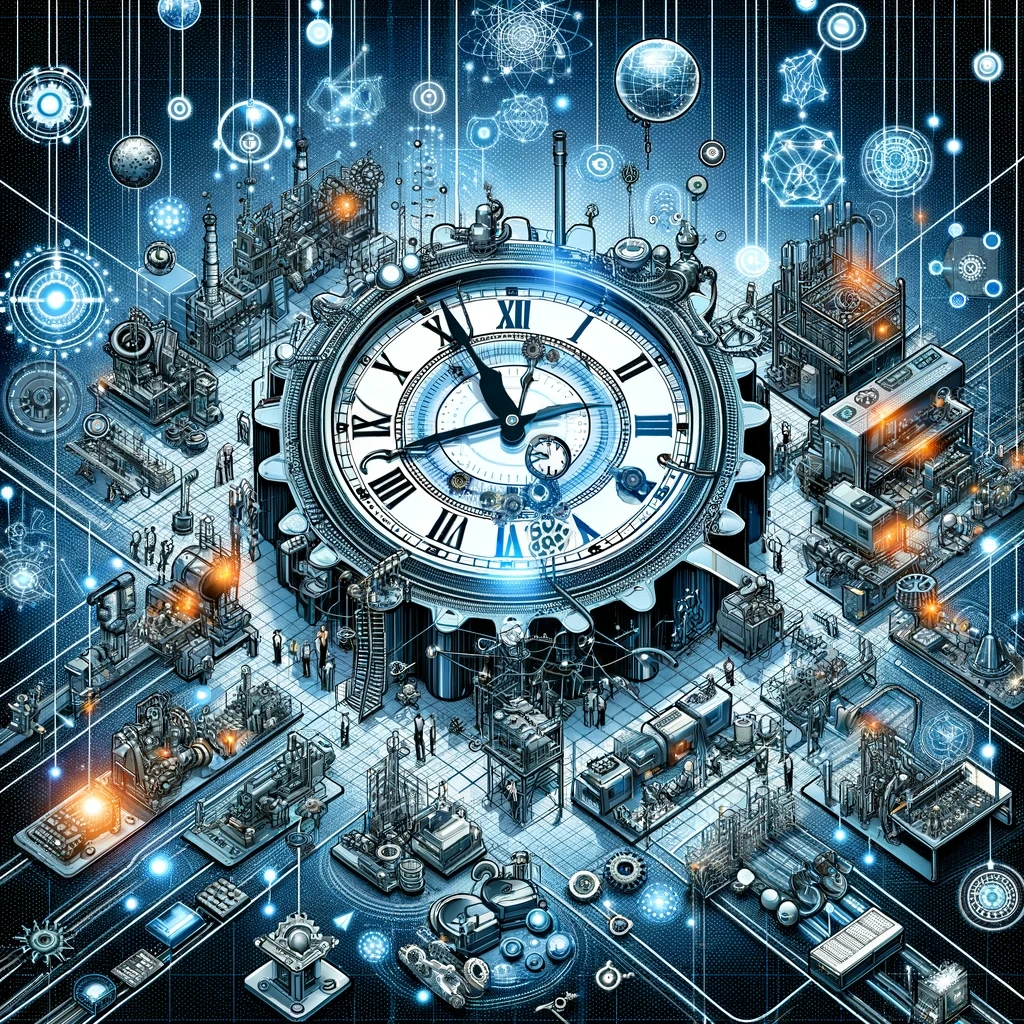
The Central Role of Scheduling in APS
Scheduling is a core element of Advanced Planning and Scheduling (APS) systems, playing a pivotal role in orchestrating the manufacturing process. It involves the meticulous planning of production activities to ensure efficient and timely completion of manufacturing orders.
Techniques for Effective Scheduling in APS
APS systems employ various sophisticated techniques for effective scheduling. These include:
1. Constraint-Based Scheduling: APS considers multiple constraints such as machine availability, labor skills, and material requirements to create realistic and achievable production schedules.
2. Sequencing and Prioritization: Orders are sequenced and prioritized based on various criteria, including due dates, customer importance, and resource availability.
3. Scenario Simulation: APS allows manufacturers to simulate different scheduling scenarios to determine the most efficient production plan.
4. Real-Time Adjustments: APS systems provide the flexibility to make real-time adjustments to schedules in response to unexpected changes or disruptions.
The role of scheduling in APS is crucial for optimizing manufacturing operations, ensuring that resources are utilized effectively and that products are delivered on time. By employing advanced techniques, APS can significantly enhance the efficiency and responsiveness of the manufacturing process.
Integrating APS Components for Optimal Performance
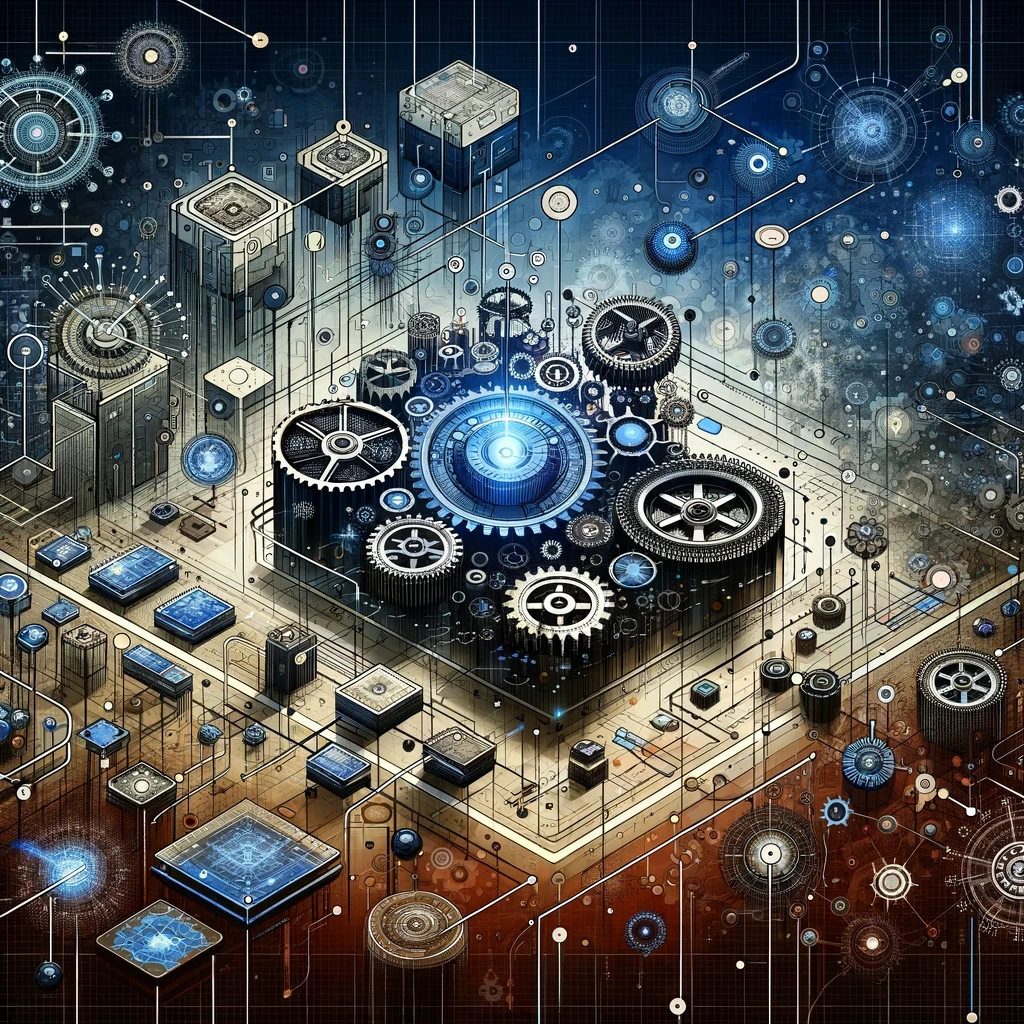
Synergy of Components in APS
The efficiency of Advanced Planning and Scheduling (APS) systems hinges on the seamless integration of its core components: demand forecasting, resource allocation, and scheduling. This integration is the linchpin that transforms individual functionalities into a cohesive, efficient whole.
The Interplay of APS Components
1. From Forecasting to Allocation: Demand forecasting predicts market needs, shaping the blueprint for resource allocation. This ensures resources are aligned with predicted demands.
2. Allocation to Scheduling: Once resources are allocated, scheduling takes over. It orchestrates the use of these resources over time, ensuring that production processes flow smoothly and efficiently.
3. Feedback Loop for Continuous Improvement: The APS system operates in a feedback loop, where post-production data inform future demand forecasting, closing the cycle of planning and execution.
The Critical Role of Integration
Integration in APS is not just about linking different components; it’s about creating a dynamic system that adapts and responds to changing conditions. This integration is key to ensuring that the manufacturing process is not only efficient but also agile and responsive to market and production dynamics.
Recent Comments