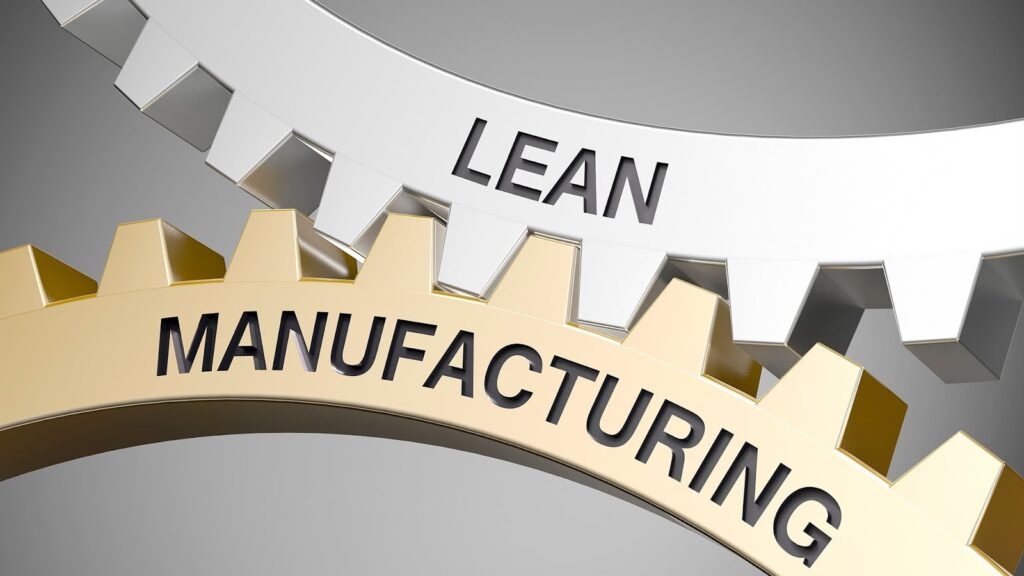
Lean Manufacturing es una filosofía de producción que busca eliminar el desperdicio en todas las etapas del proceso productivo. La manufactura en colaboración es una de las principales herramientas utilizadas dentro de la filosofía Lean para mejorar la eficiencia. En este artículo, vamos a introducirte a esta importante metodología y explicarte por qué es cada vez más popular entre las empresas modernas.
¿Qué es el Lean Manufacturing?
La teoría de LEAN manufacturing se originó en los años 40 con Taiichi Ohno, quien trabajaba para la empresa Toyota. Desde entonces, el objetivo de la gestión LEAN ha sido el de mejorar la calidad y reducir el desperdicio generado por actividades innecesarias o no evaluadas por el cliente. Aunque el término «lean manufacturing» se popularizó a finales de los 80 y principios de los 90, el enfoque lean se ha implementado en una variedad de sectores y organizaciones a lo largo de todo el mundo.
Se basa en la identificación y eliminación del desperdicio (en japonés, muda) en todas las actividades de la cadena de valor. Los objetivos principales de la metodología lean son mejorar la calidad, reducir el tiempo de entrega y los costes totales, así como mejorar la satisfacción del cliente.
Enfoques Populares
El Kaizen: Mejora continua
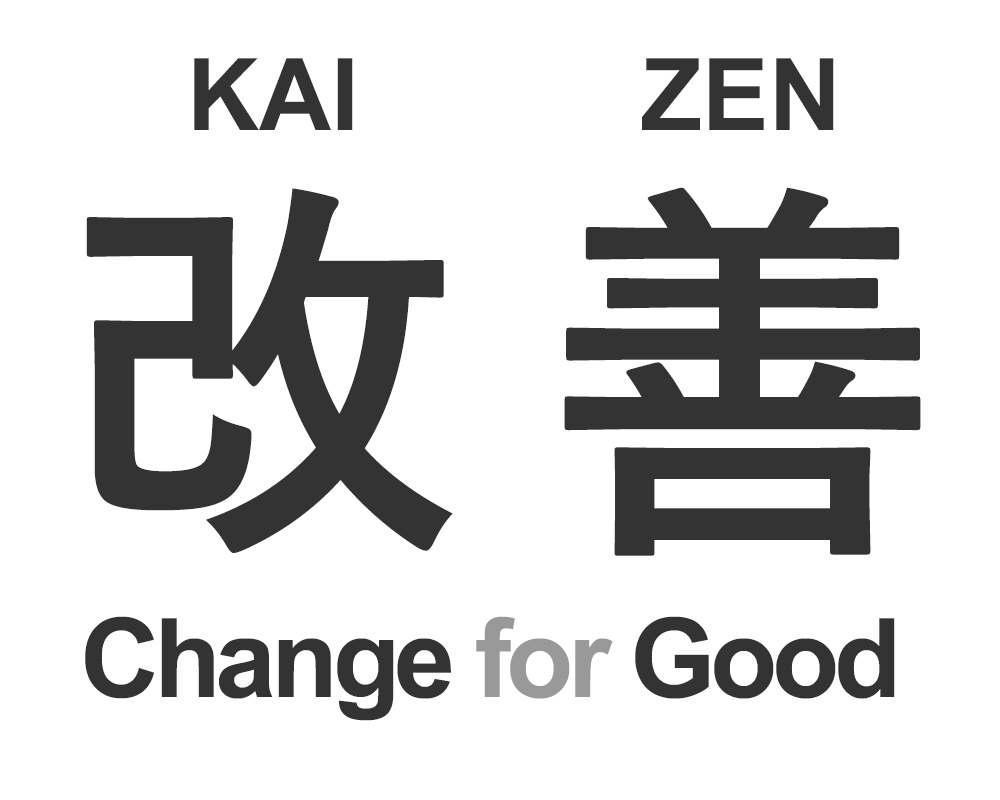
El kaizen (en japonés, cambio para mejor) es una filosofía que fomenta la mejora continua en todos los niveles y áreas de una organización. El objetivo del kaizen es establecer un ciclo sin fin de pequeñas mejoras para incrementar la eficacia general y reducir el desperdicio. La forma más común de aplicar este principio es mediante brainstorming o grupos focales para identificar áreas en las que se puede mejorar el rendimiento.
Poka-Yoke: Error Proofing o mistake proofing
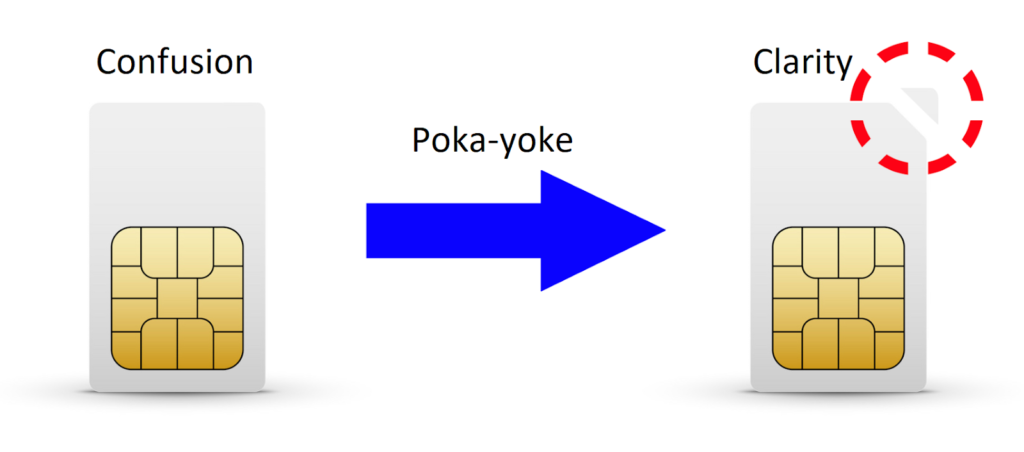
Poka-yoke (literalmente, «evitar errores» o «evitar fallos») es una técnica diseñada para prevenir o detectar errores temprano en un proceso. Existen dos tipos principales de poka-yoke: los que detectan errores antes de que tengan lugar y los que detectan errores después de que se hayan producido pero antes de que lleguen al cliente. Los dispositivos poka-yoke suelen ser simplemente ingeniosos o sorprendentemente sencillos, pero su efectividad radica en su capacidad para interrumpir el flujo del trabajo y obligar a corregir los errores antes de que se cometan.
5S: Mantener un ambiente limpio y ordenado

5S (cinco S) es un sistema japonés utilizado para mantener un ambiente limpio y ordenado. El sistema está compuesto por cinco pasos secuenciales: ordenar («seiri»), limpiar («seiton»), pulir («seiso»), estandarizar («seiketsu») y disciplina («shitsuke»). Aunque 5S comúnmente se asocia con la industria manufacturera, también puede aplicarse a oficinas, almacenes, laboratorios e incluso hogares. El principal objetivo del sistema 5S es eliminar el desperdicio generado por actividades innecesarias o no evaluadas por el cliente.
Orígenes de LEAN manufacturing
El Lean Manufacturing se originó de la cultura adoptada por las empresas japonesas, cuyo objetivo era aplicar mejoras en sus plantas de fabricación y su modelo de negocio. Ellos lograron mejorar los resultados tanto para los puestos de trabajo como para las líneas de producción. Sin embargo, no fueron los primeros en intentar optimizar la rentabilidad y eficiencia de una empresa a través del proceso productivo.
De la mano de F.W. Taylor y Henry Ford, las primeras técnicas para la optimización de la producción surgen a principios del siglo XX. Taylor estableció las bases que darían origen a la organización del trabajo más tarde, cuando Henry Ford implantó las primeras cadenas de fabricación masivas de automóviles. Estas metodologías buscaban un nuevo modelo de organización, que progresivamente se extendió al resto del mundo.
A finales del siglo XIX surgió el primer pensamiento Lean Manufacturing en Japón por parte de Sakichi Toyoda, el fundador del Grupo Toyota.

El señor Toyoda creó un aparato que detectaba problemas en los telares y anunciaba a los trabajadores con una señal cuando un hilo se rompía. La máquina de Sakichi Toyoda no sólo automatizó procesos previamente manuales, sino también agregó la actividad de la detección de error en la máquina, «Jidoka«, una máquina que cambió un proceso humano. El despliegue del productivo paraba cuando un componente fallaba, y evitaban la producción de errores. Esta medida contribuyó a que el control sobre varias máquinas estuviese centralizado en un solo operario, incrementando la productividad.
La filosofía de Toyoda, creada por el Dr. Kiichiro Toyoda, apuntaba a crear una «condición óptima de creación, en la que máquinas, instalaciones, procesos y personas trabajan juntas para incrementar valor sin generar desperdicios.» Creó metodologías y técnicas que permiten reducir los desperdicios durante las operaciones. El sistema Just-in-Time (JIT) se originó así como resultado de ello.
Fue Eiji Toyoda quien mejoró la productividad de los trabajadores aumentando la valoración del sistema JIT y estableciendo el Toyota Production System (TPS). El modelo se basaba en producir solamente lo que se necesitaba y cuando el cliente lo solicitaba, se completaba con la disminución de los tiempos de cambio de herramientas mediante el sistema SMED y diversas técnicas. Taiichi Ohno, apoyado por Eiji Toyoda, ayudó a crear las bases del espíritu Toyota para «crear las cosas», o el «Modelo Toyota».
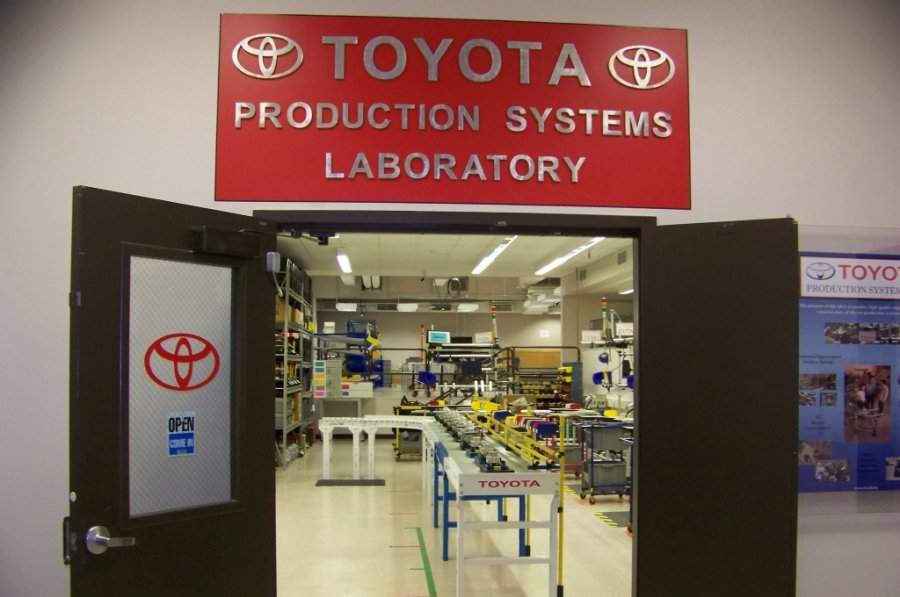
La Máquina que cambió el mundo
James Womack, Daniel Jones y Daniel Roos publicaron este libro en 1996 y ha sido una de las publicaciones más vendidas desde entonces. Se explican los fundamentos del Lean Manufacturing de forma amena, a través de la historia redirectiva de Toyota, cómo evolucionó su sistema productivo y la cultura nipona centrada en lo que respecta a fabricación.
El propósito de los tres autores, a solicitud del MIT, fue estudiar los elementos de éxito operativo y organizacional en la industria automovilística, principalmente en Japón. Buscaban investigar los factores de éxito operativo y organizational del sector automovilístico. Su trabajo duró cinco años con un costo global aproximado de 5 millones de dólares.
El libro proporciona un análisis comparativo de los procesos de fabricación entre varios proveedores, la historia de la evolución industrial desde la Revolución Industrial, las estrategias y herramientas Lean.
Producción Ajustada
- La denominada producción ajustada, en contraste con la artesanal y la masiva, es una técnica de fabricación. Gracias a esta modalidad, con la mitad del recurso humano, la mitad de la inversión económica en herramientas y equipos, con la mitad del espacio físico, se podía alcanzar los mismos objetivos que con modalidades previas.
Cero Defectos
- A la producción esbelta o ajustada se le agrega el DEFECTO CERO y otras metodologías como la fabricación multiproducto y la reducción continua de costes, con la participación de trabajadores polivalentes.
La producción ajustada precisa, en gran parte, de una distribución en planta que la facilite.
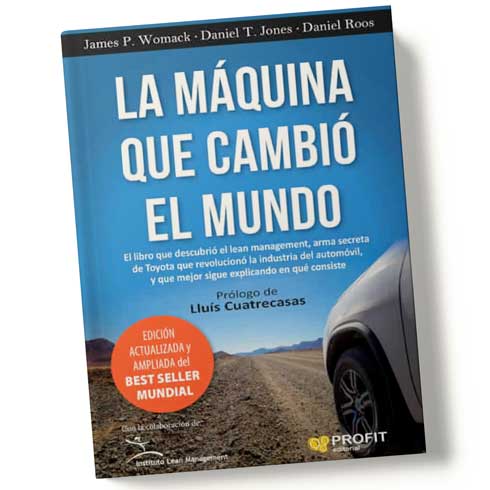
¿Cuáles son los tres ideales de Lean?
Los tres ideales de Lean Manufacturing son:
- La eliminación del desperdicio
- El flujo continuo de trabajo
- La producción en colaboración
Lean Manufacturing se centra en la reducción del desperdicio para mejorar la calidad y la productividad. El flujo continuo de trabajo permite a las empresas producir más con menos. La producción en colaboración requiere el compromiso de toda la plantilla para implementar y seguir las metodologías lean.
¿Cuáles son las 7 herramientas de Lean Manufacturing?
Las 7 herramientas de Lean Manufacturing son:
- Línea de Producción
- Just in Time (JIT)
- Kanban
- Seis Sigma
- Toyota Production System (TPS)
- 5S
- SMED
La Línea de Producción es una metodología de producción en la que las piezas se mueven en lugar de los trabajadores. La idea es que cada operario complete una tarea y luego pase la pieza al siguiente operario, lo que permite eliminar el desperdicio de tiempo y el exceso de inventario.
El Just in Time (JIT) es un sistema de producción diseñado para reducir el tiempo entre pedidos y entregas. JIT requiere que las empresas mantengan solo el inventario necesario para satisfacer la demanda inmediata, lo que significa que no hay un exceso de productos o materiales en el almacén.
Kanban es un sistema de producción visual que utiliza tableros y tarjetas para seguir el progreso de las tareas. Kanban permite a las empresas establecer límites en el número de tareas en cada fase del proceso, lo que ayuda a evitar el sobrecamino y el desperdicio.
Seis Sigma es una metodología de mejora continúa diseñada para ayudar a las empresas a reducir los defectos en sus productos y servicios. Seis Sigma establece límites estrictos en el número de errores permitidos, lo que obliga a las empresas a mejorar constantemente su calidad.
El Toyota Production System (TPS) es un sistema de producción diseñado por la compañía automotriz japonesa Toyota. TPS se centra en la eliminación de desperdicios y el flujo continuo de trabajo, lo que permite a las empresas producir más con menos.
SMED (Single-Minute Exchange of Dies) es una metodología de mejora continúa diseñada para reducir los tiempos de cambio de máquinas y equipos. SMED requiere que las empresas analicen y simplifiquen sus procesos de cambio, lo que permite a los operarios realizar el cambio en menos de diez minutos.
Estas son solo algunas de las herramientas que se utilizan en Lean Manufacturing. Para tener éxito, es importante que la empresa esté dispuesta a comprometerse con el cambio y establecer un plan para implementar las metodologías lean. La clave para el éxito es la colaboración y el trabajo en equipo, ya que ninguna herramienta funcionará si no hay un compromiso general por parte de toda la plantilla.
¿Cuáles son los 5 principios de Lean Manufacturing?
- El objetivo principal de Lean Manufacturing es reducir el desperdicio.
- Lean Manufacturing se centra en el flujo continuo de trabajo.
- Lean Manufacturing utiliza herramientas para mejorar la calidad y la productividad.
- Lean Manufacturing requiere el compromiso de toda la plantilla.
- Lean Manufacturing es un proceso de mejora continua.
El objetivo principal de Lean Manufacturing es reducir el desperdicio. Los desperdicios pueden venir en muchas formas, desde el exceso de inventario hasta los tiempos muertos en el proceso de producción. Lean Manufacturing se centra en la eliminación de estos desperdicios para mejorar la calidad y la productividad.
Lean Manufacturing utiliza herramientas como JIT, Kanban y Seis Sigma para mejorar la calidad y la productividad. JIT requiere que las empresas mantengan solo el inventario necesario para satisfacer la demanda inmediata, lo que significa que no hay un exceso de productos o materiales en el almacén. Kanban es un sistema de producción visual que utiliza tableros y tarjetas para seguir el progreso de las tareas. Seis Sigma establece límites estrictos en el número de errores permitidos, lo que obliga a las empresas a mejorar constantemente su calidad.
Para tener éxito con Lean Manufacturing, es importante que toda la plantilla esté comprometida con el cambio. Lean Manufacturing es un proceso de mejora continua, por lo que requiere el compromiso de todos para implementar y seguir las metodologías lean. La clave para el éxito es la colaboración y el trabajo en equipo.
Consejos:
- Empiece con una introducción general sobre qué es Lean Manufacturing.
- Explique cómo Lean Manufacturing se centra en la reducción del desperdicio.
- Detalle algunas de las herramientas utilizadas en Lean Manufacturing, como JIT, Kanban y Seis Sigma.
- Destaque la importancia del compromiso por parte de toda la plantilla.
- Concluya con un resumen de las claves para el éxito en Lean Manufacturing.
Consulte por nuestros asesores haciendo clic aquí