Mejora de la automatización industrial mediante simulación e ingeniería de diseño: el enfoque de Descar.tech
La automatización industrial, definida como la aplicación de sistemas de control, computadoras y tecnologías de la información para manejar y procesar operaciones industriales con una mínima intervención humana, se encuentra en el centro de las industrias de fabricación y producción modernas.

Este paradigma tecnológico permite que las máquinas y los sistemas funcionen de forma autónoma, mejorando la eficiencia, la precisión y la productividad en diversos sectores. Dentro de este marco, la ingeniería de simulación y diseño juega un papel fundamental, ofreciendo herramientas y metodologías sofisticadas para crear, probar y optimizar sistemas automatizados antes de su implementación física. Mediante la integración de estas disciplinas de ingeniería, las industrias pueden prever problemas potenciales, optimizar los procesos de producción e innovar a un ritmo sin precedentes.
Descar.tech, líder en la integración de simulación e ingeniería de diseño con automatización industrial, ejemplifica cómo esta sinergia puede conducir a avances innovadores en tecnologías de automatización. Al aprovechar el poder de la simulación y el diseño, Descar.tech crea soluciones de automatización altamente eficientes, confiables e innovadoras que impulsan a las industrias hacia adelante. Este artículo se embarca en una exploración de la intrincada relación entre la automatización industrial y la simulación y la ingeniería de diseño, mostrando cómo la experiencia de Descar.tech no solo mejora sino que revoluciona este campo dinámico.
La evolución y alcance de la automatización industrial
Breve historia y evolución de la automatización industrial.
La historia y la evolución de la automatización industrial es un viaje fascinante a través de la innovación tecnológica, marcado por hitos clave y el desarrollo de tecnologías que han cambiado fundamentalmente los procesos de fabricación y producción. Aquí hay una lista concisa que detalla esta evolución.
- Finales del siglo XVIII: la revolución industrial:
- Definición: Un período de gran industrialización donde el trabajo manual comenzó a ser reemplazado por máquinas.
- Hecho: Comenzó alrededor de 1760 en Gran Bretaña y se extendió por todo el mundo durante las siguientes décadas.
- Ejemplo: La invención de la máquina de vapor por James Watt en 1776, que impulsó las fábricas y mecanizó la producción.
- Principios del siglo XX: introducción de las líneas de montaje:
- Definición: Un proceso de fabricación en el que se agregan piezas a un producto de manera secuencial para crear un producto terminado más rápido que con los métodos tradicionales.
- Hecho: Ford Motor Company introdujo la línea de montaje en 1913, reduciendo el tiempo que llevaba construir un automóvil de más de 12 horas a dos horas y 30 minutos.
- Ejemplo: El Ford Modelo T, el primer automóvil producido en serie utilizando técnicas de línea de montaje.
- Década de 1940: máquinas de control numérico (NC):
- Definición: Máquinas controladas por un conjunto de instrucciones (códigos y números) que estaban codificadas en cinta perforada.
- Hecho: La primera máquina NC fue desarrollada en la década de 1940 por John T. Parsons en colaboración con el MIT.
- Ejemplo: Fresadoras NC, que podían cortar y dar forma con precisión a componentes metálicos.
- Década de 1970: controladores lógicos programables (PLC):
- Definición: Computadoras digitales industriales diseñadas para el control de procesos de fabricación, como líneas de montaje o dispositivos robóticos.
- Hecho: El primer PLC, el Modicon 084, fue introducido en 1969 por Dick Morley.
- Ejemplo: Los PLC se utilizan en diversas industrias para tareas de automatización, desde el control de maquinaria en líneas de montaje de fábricas hasta accesorios de iluminación.
- Década de 1980: Introducción de la robótica.:
- Definición: Máquinas programables capaces de realizar una serie compleja de acciones de forma automática, especialmente una programable por computadora.
- Hecho: En 1980, Unimation introdujo con General Motors el robot PUMA (Máquina universal programable para ensamblaje).
- Ejemplo: Robots industriales utilizados en la fabricación de automóviles para soldar y ensamblar piezas.
- Década de 1990: Fabricación integrada por computadora (CIM):
- Definición: El enfoque de fabricación de utilizar computadoras para controlar todo el proceso de producción.
- Hecho: Este concepto ganó importancia a finales de los 80 y principios de los 90, integrando varias tecnologías como CAD/CAM y ERP.
- Ejemplo: Fábricas totalmente automatizadas donde los datos de diseño se utilizan directamente para controlar la maquinaria.
- Década de 2000: Industria 4.0:
- Definición: Nombre que recibe la tendencia actual de automatización e intercambio de datos en las tecnologías de fabricación, incorporando sistemas ciberfísicos, Internet de las cosas, computación en la nube y computación cognitiva.
- Hecho: El término se introdujo por primera vez en la Feria de Hannover en 2011.
- Ejemplo: Fábricas inteligentes donde las máquinas y los sistemas están conectados digitalmente a lo largo de toda la cadena de producción, lo que permite el análisis de datos y la toma de decisiones en tiempo real.
- Década de 2010 y más allá: Inteligencia artificial (IA) y aprendizaje automático en la automatización:
- Definición: La IA se refiere a la simulación de la inteligencia humana en máquinas que están programadas para pensar como humanos e imitar sus acciones. El aprendizaje automático es una aplicación de IA que proporciona a los sistemas la capacidad de aprender y mejorar automáticamente a partir de la experiencia.
- Hecho: La IA y el aprendizaje automático se han convertido en parte integral del avance de la automatización industrial, con un crecimiento significativo en las aplicaciones observado en la década de 2010.
- Ejemplo: Mantenimiento predictivo, donde los algoritmos de IA predicen cuándo la maquinaria requerirá mantenimiento y dan servicio preventivo al equipo para evitar tiempos de inactividad.
Esta cronología destaca los principales hitos en la evolución de la automatización industrial y muestra cómo los avances tecnológicos han automatizado progresivamente los procesos de fabricación y producción para mejorar la eficiencia, la calidad y la productividad.
Definicion de Sistemas de control
Un sistema de control es un conjunto de dispositivos y herramientas de gestión que monitorean y controlan maquinaria o procesos para lograr los resultados deseados. Opera según el principio de control de retroalimentación, donde los datos del sistema se monitorean continuamente y se utilizan para realizar ajustes en las variables de control, manteniendo el rendimiento del sistema en los parámetros establecidos. Los sistemas de control pueden ser simples, como un termostato que mantiene la temperatura ambiente, o complejos, como los que gestionan las operaciones de una central nuclear. Son fundamentales en diversas aplicaciones, incluidas la fabricación, la aviación, la automoción y los sistemas de gestión de edificios, garantizando eficiencia, seguridad y confiabilidad.
Definicion de Automatización industrial
La automatización industrial se refiere al uso de sistemas de control, como computadoras o robots, y tecnologías de la información para manejar diferentes procesos y maquinarias en una industria para reemplazar a un ser humano. Es la aplicación de control automático al proceso de fabricación para aumentar la productividad y reducir el error humano. La automatización industrial integra diversas tecnologías, incluidos PLC (controladores lógicos programables), sistemas SCADA (control de supervisión y adquisición de datos) y DCS (sistemas de control distribuido), para crear procesos de producción altamente eficientes y precisos. Esta tecnología permite a las industrias lograr una producción en masa, una mejor calidad del producto y una mayor seguridad, al tiempo que reducen los costos laborales y el tiempo de producción.
¿Cuál es el Uso de la Automatización Industrial?
La automatización industrial se emplea para mejorar la eficiencia operativa, la seguridad y la calidad del producto en la fabricación. Sus usos incluyen aumentar la productividad al permitir ciclos de producción las 24 horas del día, los 7 días de la semana, garantizar una calidad constante, reducir los costos operativos mediante el uso eficiente de los recursos, mejorar la seguridad en el lugar de trabajo mediante el manejo de tareas peligrosas y facilitar la toma de decisiones basada en datos. Esta tecnología respalda la escalabilidad y reduce los costos laborales, lo que en última instancia conduce a procesos de fabricación innovadores y competitivos.
“La automatización de procesos industriales implica instrumentación, control, interfaz humana y subsistemas de comunicación, lo que garantiza una producción de calidad, consistente y rentable”.
K.l.s. Sharma. «Descripción general de la automatización de procesos industriales». (2011)
Beneficios de la automatización industrial
La automatización industrial transforma la fabricación moderna a través de un conjunto de beneficios: aumenta sustancialmente la productividad al permitir la operación continua, garantiza una calidad constante del producto con precisión, mejora la seguridad en el lugar de trabajo al asumir tareas peligrosas, logra eficiencia de costos a través de operaciones optimizadas, mejora la recopilación de datos para tomar mejores decisiones. fabricación, permite una fácil escalabilidad para satisfacer las demandas fluctuantes y reduce el impacto ambiental al minimizar el desperdicio y optimizar el uso de energía. Estas ventajas subrayan colectivamente el papel fundamental de la automatización para impulsar la eficiencia económica, la seguridad y la sostenibilidad en el sector industrial.
- Productividad incrementada: La automatización eleva la capacidad de producir bienes de manera más eficiente, permitiendo el funcionamiento continuo de los procesos de fabricación las 24 horas del día. Por ejemplo, una instalación de embotellado automatizada puede aumentar significativamente su producción en comparación con las operaciones manuales, garantizando que la producción nunca tenga que detenerse.
- Calidad consistente: Con alta precisión y mínima variación en las tareas, los sistemas automatizados garantizan que cada producto cumpla con los mismos estándares de alta calidad. Esto es crucial en sectores como la fabricación de automóviles, donde el ajuste preciso de las piezas es esencial para la seguridad y el rendimiento del vehículo.
- Seguridad mejorada: Al asumir tareas peligrosas y trabajar en entornos peligrosos, la automatización reduce los accidentes laborales y protege a los empleados. La robótica en la fabricación de productos farmacéuticos, por ejemplo, puede manejar sustancias químicas tóxicas, mitigando la exposición humana a sustancias potencialmente dañinas.
- Eficiencia de costo: A través de operaciones optimizadas, la automatización conduce a reducciones significativas en los costos de producción. En la industria de procesamiento de alimentos, la automatización no solo minimiza el desperdicio sino que también optimiza el uso de energía, lo que contribuye a reducir los gastos operativos.
- Recopilación de datos mejorada: La capacidad de monitorear y registrar una amplia gama de variables de proceso en tiempo real permite una recopilación completa de datos. Las fábricas inteligentes aprovechan los sensores y los dispositivos IoT para realizar un seguimiento del rendimiento de las máquinas, lo que facilita un enfoque proactivo del mantenimiento y la eficiencia.
- Escalabilidad: La flexibilidad de los sistemas automatizados para aumentar o reducir la producción en función de la demanda garantiza que las empresas puedan ajustar su producción sin incurrir en tiempos de inactividad significativos ni costos adicionales. Los almacenes de comercio electrónico son un ejemplo de esto, ya que utilizan sistemas automatizados para gestionar volúmenes de pedidos fluctuantes con facilidad.
- Impacto ambiental reducido: La automatización contribuye a la sostenibilidad optimizando el consumo de energía y reduciendo los residuos. Las instalaciones industriales que incorporan sistemas automatizados de gestión de energía ejemplifican cómo la tecnología puede desempeñar un papel fundamental a la hora de minimizar la huella ecológica y promover la gestión ambiental.
A través de estos aspectos, la automatización industrial demuestra ser una piedra angular de la fabricación moderna, ofreciendo no sólo beneficios económicos sino también mejorando la seguridad y la sostenibilidad ambiental.
Los 4 Tipos de automatización industrial
Las tecnologías de automatización industrial se pueden clasificar en cuatro tipos principales, que se distinguen por su flexibilidad, escalabilidad y especificidad de aplicación. Estas categorías desempeñan un papel fundamental a la hora de determinar la estrategia de automatización adecuada para un proceso de fabricación o línea de producción.
1. Automatización fija (Automatización dura)
- Descripción general: La automatización fija implica el uso de equipos que están configurados para realizar una tarea específica. Se caracteriza por altas tasas de producción y normalmente se utiliza para la producción en masa de un solo tipo de producto.
- Solicitud: Un ejemplo de automatización fija es una línea de montaje de cinta transportadora diseñada específicamente para la fabricación de un único modelo de automóvil. Este sistema es eficiente pero carece de la flexibilidad para adaptarse a diferentes productos sin una reconfiguración significativa.
2. Automatización programable
- Descripción general: La automatización programable permite la reprogramación de la maquinaria para adaptarse a diferentes configuraciones de productos. Este tipo de automatización es adecuado para la producción por lotes donde las especificaciones del producto cambian con frecuencia.
- Solicitud: Un sistema de soldadura robótica que se puede reprogramar para diferentes tipos de soldaduras en varios modelos de automóviles ilustra la automatización programable. Ofrece más flexibilidad que la automatización fija, pero requiere tiempo de inactividad para la reprogramación.
3. Automatización flexible (Automatización suave)
- Descripción general: Los sistemas de automatización flexibles están diseñados para gestionar una variedad de tareas con un tiempo de inactividad mínimo o nulo para los cambios. Estos sistemas son altamente adaptables, lo que permite cambios rápidos entre tipos de productos.
- Solicitud: Un sistema de fabricación equipado con máquinas CNC que pueden cambiar rápidamente entre diferentes operaciones de mecanizado para pequeñas tiradas de producción de piezas personalizadas es un ejemplo de automatización flexible. Combina la eficiencia de la automatización fija con la adaptabilidad de la automatización programable.
4. Automatización integrada
- Descripción general: La automatización integrada implica el funcionamiento integral y coordinado de varios sistemas automatizados a lo largo de todo el proceso de producción. Este tipo implica el uso de tecnologías avanzadas como IoT (Internet de las cosas), IA (Inteligencia artificial) y aprendizaje automático para un funcionamiento perfecto.
- Solicitud: Una fábrica totalmente automatizada donde los robots, los transportadores y las máquinas CNC están conectados a través de un sistema de control central, capaz de ajustar de forma autónoma las operaciones en función de los datos de oferta y demanda en tiempo real, ejemplifica la automatización integrada.
Estos cuatro tipos de automatización industrial ofrecen distintos grados de flexibilidad, eficiencia y complejidad, brindando soluciones para cada escala y alcance de las necesidades de fabricación.
Los 3 Principales Sistemas utilizados en la automatización industrial
La implementación de la automatización industrial se basa en varios sistemas centrales que facilitan el control, seguimiento y ejecución de los procesos de fabricación.
1. Controladores lógicos programables (PLC)
- Descripción general: Los PLC son sistemas computarizados especializados diseñados para entornos industriales. Se utilizan para controlar una amplia gama de maquinaria y procesos, ofreciendo robustez, flexibilidad y facilidad de programación. Los PLC leen entradas de sensores o entradas manuales, procesan estas entradas de acuerdo con la lógica programada y activan salidas para controlar actuadores o indicadores.
- Solicitud: En una línea de ensamblaje automotriz, los PLC pueden controlar el funcionamiento de brazos robóticos, cintas transportadoras y equipos de pintura, ajustando las operaciones en tiempo real según los requisitos de producción específicos.
2. Sistemas de Supervisión, Control y Adquisición de Datos (SCADA)
- Descripción general: Los sistemas SCADA se utilizan para el seguimiento y control remoto de procesos industriales. Estos sistemas recopilan datos de sensores en varias ubicaciones, envían los datos a un sistema informático central y luego muestran esta información en las pantallas del operador. Los sistemas SCADA permiten a los operadores ajustar los controles de procesos de forma remota, optimizando el rendimiento y detectando problemas potenciales de manera temprana.
- Solicitud: En una instalación de tratamiento de agua, los sistemas SCADA pueden monitorear y ajustar los niveles de tratamiento químico, caudales y capacidades de almacenamiento en diferentes etapas del proceso, asegurando la calidad del agua y la eficiencia del sistema.
3. Sistemas de control distribuido (DCS)
- Descripción general: Los DCS se utilizan principalmente en procesos complejos que se extienden por amplias ubicaciones geográficas. Este sistema consta de un controlador central que se comunica con una red de unidades controladoras descentralizadas, gestionando las operaciones de distintas secciones del proceso. DCS es conocido por su alta confiabilidad y capacidades de control en tiempo real, lo que lo hace ideal para procesos que requieren control preciso y seguridad operativa.
- Solicitud: En la industria petroquímica, un DCS podría controlar el proceso de refinación, garantizando una temperatura, presión y caudales óptimos en toda la red de tuberías y cámaras de reacción para maximizar la producción y la seguridad.
Estos tres sistemas principales (PLC, SCADA y DCS) forman la columna vertebral de la automatización industrial y cada uno cumple funciones distintas, desde el control directo de la máquina hasta la gestión remota de procesos y el control integrado de procesos en amplias áreas. Su implementación es fundamental para mejorar la productividad, garantizar la calidad y lograr escalabilidad en las operaciones industriales modernas.
¿Qué industrias utilizan más automatización?
Varias industrias están a la vanguardia en la integración de la automatización en sus operaciones, aprovechando significativamente la tecnología para mejorar la eficiencia, la productividad y la seguridad. Los sectores que más utilizan la automatización incluyen:
- Automotor: Reconocido por su alto grado de automatización, desde líneas de montaje hasta robots de pintura y soldadura, asegurando precisión y eficiencia.
- Fabricación de electrónica y semiconductores: Utiliza la automatización para procesos complejos de ensamblaje, pruebas y embalaje para satisfacer las demandas de producción de gran volumen con precisión.
- Alimentos y bebidas: Emplea automatización para el embalaje, la clasificación y el procesamiento para garantizar la coherencia, la seguridad y la escalabilidad en la producción.
- Productos farmacéuticos: Utiliza la automatización en la formulación, el envasado y el control de calidad de los medicamentos para cumplir con estrictos estándares regulatorios y mejorar la seguridad del producto.
- Petróleo y gas: Aprovecha la automatización de las operaciones de exploración, perforación y refinería para mejorar la seguridad y la eficiencia en entornos peligrosos.
Estas industrias destacan las diversas aplicaciones de la automatización, mostrando su papel fundamental en la mejora de la productividad y la eficiencia operativa en varios sectores.
Niveles de automatización industrial
El nivel más alto de automatización industrial a menudo se caracteriza por la integración y coordinación de varios sistemas avanzados que facilitan el funcionamiento, el flujo de datos y la toma de decisiones sin problemas en todo el espectro de la cadena de fabricación y suministro. Entre estos sistemas, los Sistemas de Ejecución de Manufactura (MES), Gestión de operaciones de fabricación (MOM), Planificación de recursos empresariales (ERP) y Planificación y programación avanzadas (APS) desempeñan papeles fundamentales.
MES (Sistemas de ejecución de fabricación)
- MES opera a nivel de planta, gestionando y monitoreando el proceso de producción en tiempo real. Garantiza que las operaciones de fabricación se ejecuten de forma eficaz, optimizando la producción y manteniendo los estándares de calidad.
MOM (Gestión de Operaciones de Fabricación)
- MOM abarca un alcance más amplio que MES, integrando varios aspectos del proceso de fabricación, desde la producción hasta la calidad y el mantenimiento. Proporciona una visión general y un control completos de todas las operaciones de fabricación.
ERP (planificación de recursos empresariales)
- Los sistemas ERP integran todas las facetas de una empresa en un sistema de información integral al que pueden acceder las personas de toda la organización. Cubre finanzas, recursos humanos, adquisiciones, gestión de la cadena de suministro y más, lo que facilita operaciones optimizadas y planificación estratégica.
APS (Planificación y programación avanzada)
- Los sistemas APS se utilizan para la planificación y programación de la producción, optimizando el uso de los recursos de fabricación para satisfacer la demanda. Las herramientas APS consideran la capacidad de producción, la disponibilidad de materiales y las limitaciones operativas para generar programas de producción eficientes.
El más alto nivel de automatización industrial: enfoque de sistemas integrados
El nivel más alto de automatización industrial se logra cuando estos sistemas (MES, MOM, ERP y APS) están completamente integrados, lo que permite un flujo fluido de información y una toma de decisiones coordinada desde el piso de producción hasta el piso superior. Este enfoque holístico garantiza que la planificación estratégica (ERP) se alinee con la ejecución operativa (MES y MOM) y se optimice mediante la programación inteligente (APS), lo que da como resultado un entorno de fabricación ágil, receptivo y altamente eficiente. Este nivel de integración representa el pináculo de la automatización industrial, donde la tecnología y la gestión de procesos convergen para crear fábricas inteligentes capaces de adaptarse a las cambiantes demandas del mercado y los desafíos operativos en tiempo real.
La importancia de la ingeniería de diseño y simulación en la automatización industrial
La ingeniería de simulación y diseño son disciplinas fundamentales dentro del sector industrial, particularmente en el ámbito de la automatización. Estos campos combinan principios teóricos de ingeniería con aplicaciones prácticas, aprovechando software y metodologías avanzadas para visualizar, probar y refinar procesos y productos antes de su fabricación física. Su importancia abarca varias facetas de la automatización industrial, desde la conceptualización hasta la optimización, y encarna una combinación de creatividad, precisión y destreza tecnológica.
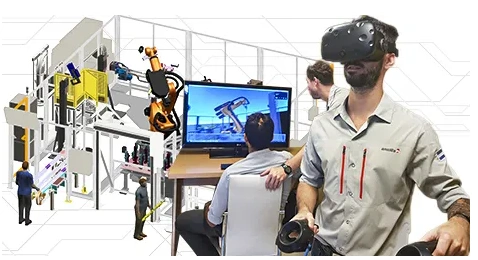
Ingeniería de simulación Es el proceso de utilizar modelos basados en computadora para simular el comportamiento físico y funcional de productos o procesos potenciales. Permite a los ingenieros analizar una amplia gama de escenarios y condiciones operativas, identificando problemas potenciales y oportunidades de mejora sin la necesidad de prototipos físicos. Este campo de pruebas virtual es esencial para explorar el comportamiento de sistemas complejos, como dinámica de fluidos, termodinámica, tensión mecánica y más, dentro de un entorno controlado y libre de riesgos.
Ingeniería de diseño se centra en la conceptualización y planificación detallada de productos y sistemas. Implica crear especificaciones, dibujos y planos precisos que sirvan como planos para la fabricación. Esta disciplina integra varios principios de ingeniería y metodologías de diseño para desarrollar productos innovadores, funcionales y factibles. La ingeniería de diseño es fundamental para transformar ideas en productos tangibles, garantizando que cada aspecto, desde la funcionalidad hasta la estética, se considere meticulosamente.
Importancia en la automatización industrial
La integración de la simulación y la ingeniería de diseño en la automatización industrial es transformadora y ofrece beneficios incomparables:
- La innovación y la creatividad: Estos procesos fomentan una cultura de innovación, permitiendo la exploración de nuevas ideas y soluciones más allá de las limitaciones tradicionales. Los ingenieros pueden experimentar con diferentes materiales, configuraciones y procesos para descubrir métodos de producción más eficientes, rentables y confiables.
- Eficiencia y Optimización: La simulación y la ingeniería de diseño contribuyen significativamente a la eficiencia de las líneas de producción. Al identificar cuellos de botella, optimizar la asignación de recursos y optimizar los procesos mediante pruebas virtuales, estas disciplinas ayudan a crear entornos de fabricación más eficientes y productivos.
- Reducción de riesgos y seguridad: La implementación de cambios en modelos virtuales reduce significativamente los riesgos asociados con modificaciones directas a sistemas activos. Este enfoque preventivo garantiza la seguridad y la integridad operativa al permitir pruebas exhaustivas antes de la implementación.
- Ahorro de costes: La capacidad de detectar problemas y optimizar los diseños en las primeras etapas de la fase de desarrollo genera ahorros de costos sustanciales. Al reducir la necesidad de prototipos físicos, minimizar el desperdicio de material y evitar costosas modificaciones posteriores a la producción, la simulación y la ingeniería de diseño contribuyen a prácticas de fabricación más sostenibles desde el punto de vista económico.
- Integración interdisciplinaria: Estos procesos de ingeniería fomentan la colaboración entre diferentes disciplinas de ingeniería, asegurando que todos los aspectos del sistema de automatización estén bien coordinados e integrados. Este enfoque holístico mejora la funcionalidad general y la confiabilidad de los sistemas automatizados.
En esencia, la simulación y la ingeniería de diseño son indispensables en la evolución y perfeccionamiento de los sistemas de automatización industrial. Permiten al sector industrial navegar por las complejidades de las demandas de fabricación modernas, impulsando innovaciones que remodelan el panorama de la producción y la eficiencia de la fabricación. A través de una planificación detallada, pruebas rigurosas y resolución creativa de problemas, estas disciplinas sientan las bases para el futuro de la automatización industrial, caracterizada por operaciones más inteligentes, seguras y sostenibles.
Integración: ingeniería de simulación y diseño en automatización industrial
La integración de la simulación y la ingeniería de diseño con la automatización industrial marca un avance fundamental en la fabricación, caracterizado por el enfoque innovador de Descar.tech. Esta sección describe la esencia de esta integración y su impacto en la industria.
La integración de la simulación y la ingeniería de diseño en la automatización industrial es crucial para mejorar la precisión, la eficiencia y la adaptabilidad en los procesos de fabricación, allanando el camino para la creación de gemelos digitales y simulaciones sofisticadas.
Componentes centrales de la integración
Descar.tech aprovecha tecnologías y metodologías de última generación, incluido el modelado 3D y el análisis computacional, para predecir y optimizar los resultados de fabricación, fusionando la creatividad con la precisión de la ingeniería.
Aplicaciones del mundo real y estudios de casos
Descar.tech ha demostrado éxito en varios proyectos, como la optimización de líneas de montaje automatizadas para fabricantes de automóviles, mostrando las ventajas prácticas de este enfoque integrado.
El enfoque único de Descar.tech
Distinguida por su adopción holística de la Industria 4.0, Descar.tech integra IoT, IA y metodologías colaborativas para desarrollar soluciones de automatización adaptables y con visión de futuro.
Direcciones futuras de la integración
La integración liderada por Descar.tech no sólo significa un salto en las capacidades de fabricación sino que también establece un punto de referencia para futuros avances en la automatización industrial.
Para más detalles o ponerse en contacto con Descar,
puede contactarlos al +54 9 351 560 8436 o enviarles un correo electrónico a info@descar.tech